1. Definition of rubber roller:
Rubber roller is made of metal or other materials as the core, covered with rubber by vulcanization and made of roll products.
2. The classification of rubber rollers:
According to the use can be divided into: paper roller, printing and dyeing rollers, printing rollers, hulling rollers, metallurgical rollers and oil printing rollers;
According to the surface morphology can be divided into: flat rollers and patterned rollers;
According to the material can be divided into: butyl rubber roller, nitrile rubber roller, polyurethane rubber roller and silicone rubber roller. Rubber rollers are generally composed of outer rubber, hard rubber layer, metal core, roll neck and ventilation holes, and its processing includes core sandblasting, adhesive treatment, adhesive molding, wrapping, wire winding, vulcanizing tank vulcanization and surface processing and other processes. Mainly used in papermaking, printing and dyeing, printing, grain processing, metallurgy, plastics processing and so on.
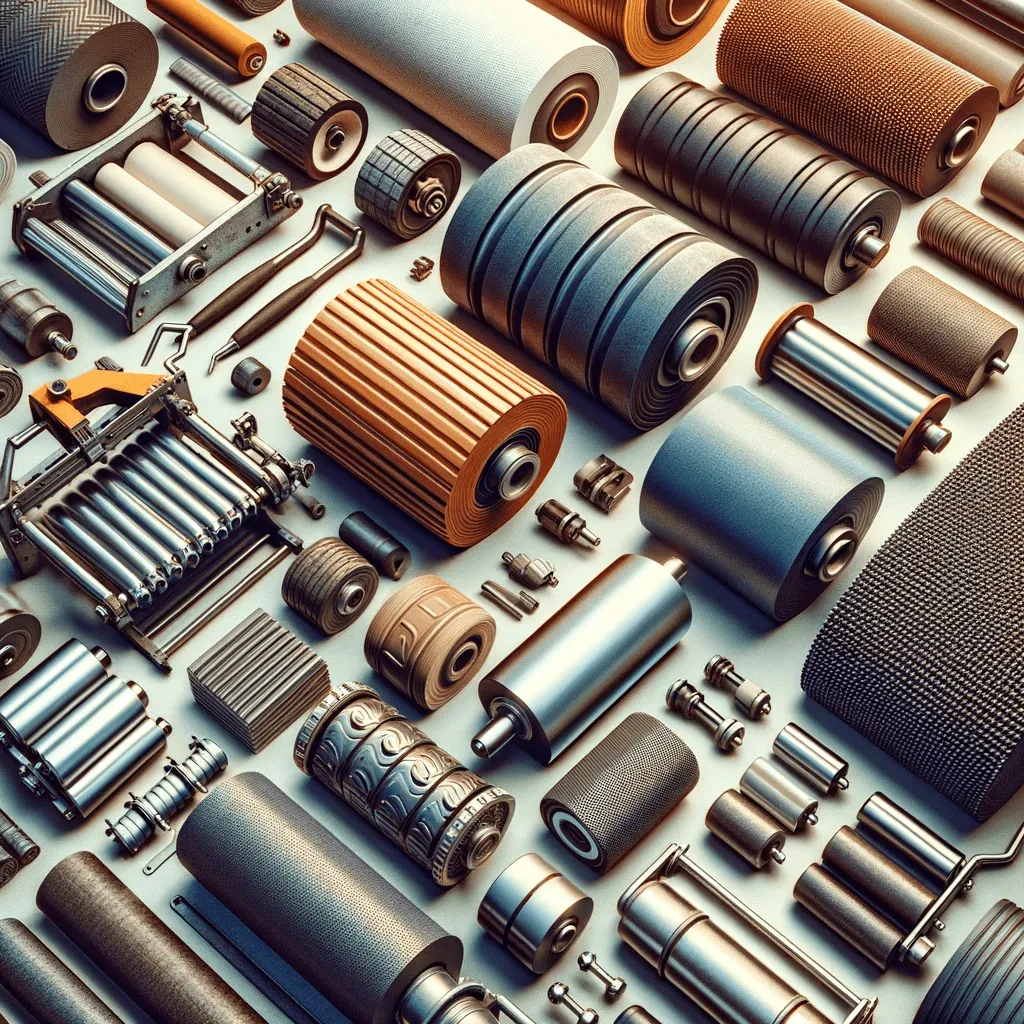
3. The rubber roller production process and technical explanations
In recent years, injection, extrusion and winding technology continues to develop, roller molding and vulcanization equipment so that roller production has gradually embarked on mechanization and automation. Roller performance on the whole machine has a huge impact on the process operation and production quality is extremely strict, and many of its products have been classified as a category of fine products, of which the selection of rubber, plastic materials and product size precision control is the key. Rubber roller rubber surface does not allow any impurities, trachoma and bubbles, not to mention scars, defects, grooves, cracks and local sponges and soft and hard different phenomena.
For this reason, the rubber rollers are required to maintain absolute cleanliness and fine work throughout the production process to achieve uniformity of operation and standardization of technology. Rubber plastic and metal core combination, paste and injection molding, vulcanization and grinding processes have thus become highly technical process.
4. The production process flow chart of the rubber roller
1. Rubber preparation
For rubber rollers, rubber mixing is the most critical link. Rubber roller with rubber from natural rubber, synthetic rubber to special materials up to more than 10 kinds of more than the rubber content of 25% to 85%, hardness for the earth (0 ~ 90) degrees, across a wide range. Therefore, how to make these rubber mixing uniform has become a major problem. The conventional method is to use the opening machine to a variety of mother refining rubber in the form of mixing and processing. In recent years, more companies have switched to the use of meshing type of refiner, in order to segmented mixing way to produce rubber.
After the rubber material to achieve uniform mixing, but also with the rubber filtering machine to filter the rubber, to eliminate impurities in the rubber material. Then use the calender, press out machine, laminating machine into no bubbles and impurities in the film or strip for roll molding.
2. Molding
Rubber roll molding is mainly in the metal core paste covered rubber, there are packages of paste method, extrusion method, molding method, injection pressure method and injection method, etc.. At the same time, in the molding process to microcomputer automatic control of its specifications and the appearance of the shape, some can also be used to press out of the machine at right angles and shaped extrusion method for molding.
Small and miniature rubber rollers can be hand-patched, extruded into the set, injection pressure, injection and pouring and other forms of production processes. In order to improve production efficiency, now most of the molding method, and the accuracy is much higher than the non-molding method.
3. Vulcanization
At present, large and medium-sized rubber roller vulcanization is still vulcanizing tank vulcanization, although the flexible pressure mode has changed, but still not out of the round-trip transport lifting and unloading of the heavy labor burden. Vulcanization heat source has steam, hot air and hot water in three heating methods, the mainstream is still steam. Because of the metal core contact with water vapor and special requirements of the roll, the use of indirect steam vulcanization, time to extend 1 to 2 times, generally used in hollow iron core roll. Can not use the vulcanizing tank vulcanization of special rubber rolls, sometimes take hot water vulcanization, but the treatment of water pollution to be resolved.
In order to prevent the rubber and metal core due to differences in thermal conductivity to produce different shrinkage caused by the roll and the rubber core between the occurrence of delamination, the general vulcanization of more than a slow rise in temperature and pressure, the vulcanization time is far longer than the rubber itself required vulcanization time is much longer. Large rubber rollers in order to achieve uniform vulcanization inside and outside as well as to make the metal core and rubber with similar thermal conductivity, often stay in the tank for as long as 24 ~ 48h, about 30 ~ 50 times the normal vulcanization time of rubber.
4. Surface treatment
Surface treatment is the last and most critical process of rubber roller production, surface grinding state directly around the use of rubber roller performance. Currently grinding a variety of methods, but mainly mechanical turning and grinding, grinding methods, grinding tools and abrasives used is very important, the enterprises regarded as technical know-how, to maintain the attitude of the foreign not announced. One of the biggest problems is how to solve the grinding of rubber heat phenomenon and maintain the best deflection of the surface after grinding.
Rubber rollers in addition to the surface to be abrasive treatment, but also thoroughly cleaned to remove the surface attached to the rubber powder, the higher requirements of the surface to be further polished, but also in the surface coating resin coatings, latex paints, magnetic powders, static powders and so on. At the same time, can also be plated a layer of the required plating, or chemical oxidation treatment, etc., in order to achieve the purpose of light sensing, corrosion resistance, magnetization and conductivity and other functions.
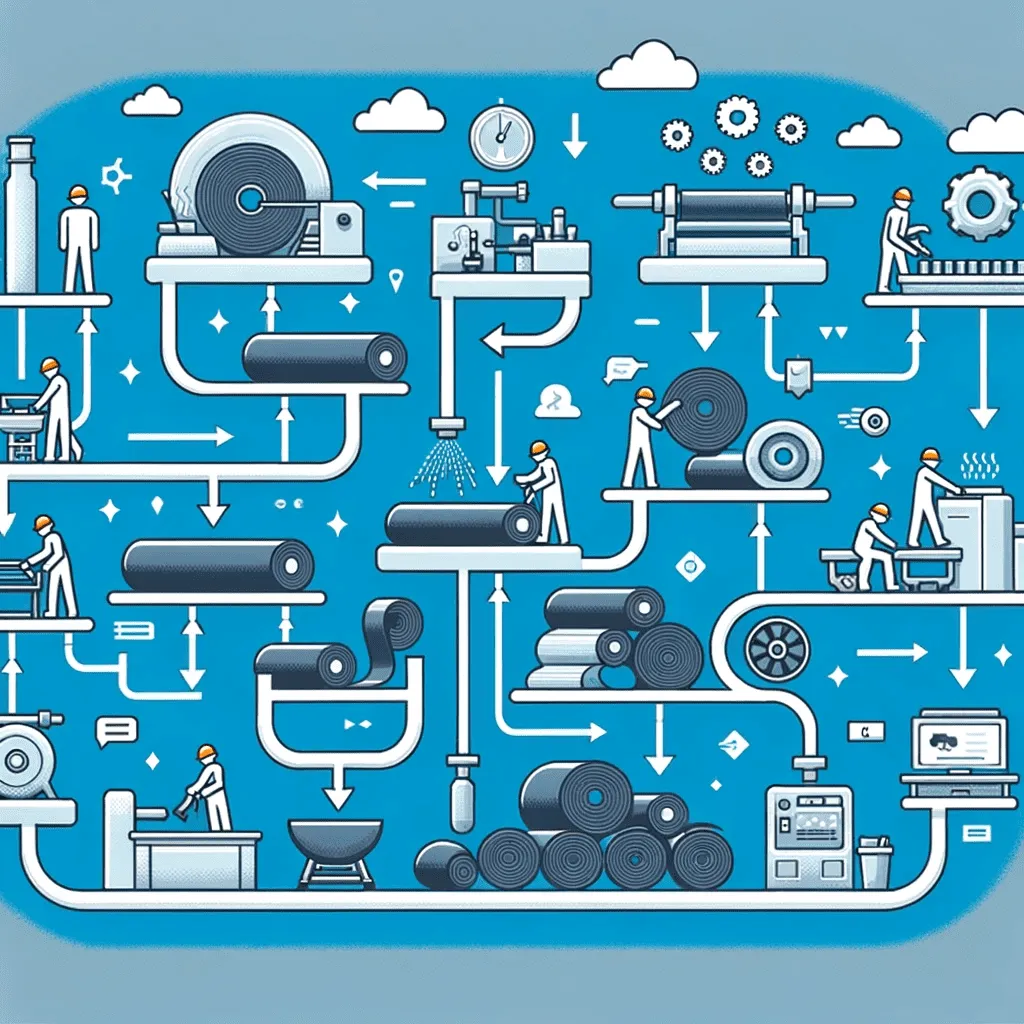
The main raw materials of rubber rollers: rubber and other polymers, vulcanizing agents, plasticizers, fillers, accelerators
Its main process and role: mixing - filtration - curing treatment - grinding - polishing
- Mixing:Control the content of each component, hot baking temperature, etc., so that the hardness and composition stabilization.
- filtration: to make the colloid uniform and free of impurities. This is particularly important for high-speed printing machine: in high-speed operation of the force is uniform, the transfer of energy is uniform due to a variety of factors caused by expansion or contraction, but still be able to maintain uniformity and consistency, so that only rely on the regulation can be mitigated or avoid adverse effects.
- curing: through heating and pressure and vulcanization treatment, stabilizing the speed increaser, so that the rubber by external forces when the contraction is reduced to a minimum. Will be fluffy and ductile performance of the compound into a solid, but with a certain degree of softness of the material, so that more suitable for the transfer of ink and transfer.
- grinding and polishing: the key to determine the dimensional accuracy and surface area of the rubber roller, especially the curvature of the alcohol water roller processing. The rubber surface appears to be smooth, but under high magnification, there are many tiny bumps and concave parts. These raised and concave parts increase the surface area of the rubber roller, making it superior ink transfer, transfer performance.