Introduction:
This report analyzes the global rubber roller industry from perspectives of market capacity, raw material supply, downstream demand shifts, competitive landscape change and substitute technology trends; providing key insights and forecasts.
Market Size Analysis
The global rubber roller market was valued at $18.2 billion in 2022, reflecting steady growth of 6% annually. This robust expansion is attributed to sustained downstream demand in printing & packaging, textiles, pharmaceuticals, metals processing and other key industries. Asia Pacific makes up over 60% of total global production volume, making it the undisputed manufacturing hub.
Industry consultants predict over 5% CAGR growth through 2025, surpassing $21 billion in market value. As emerging economies ramp up manufacturing and exports, rubber rollers will see continued adoption.
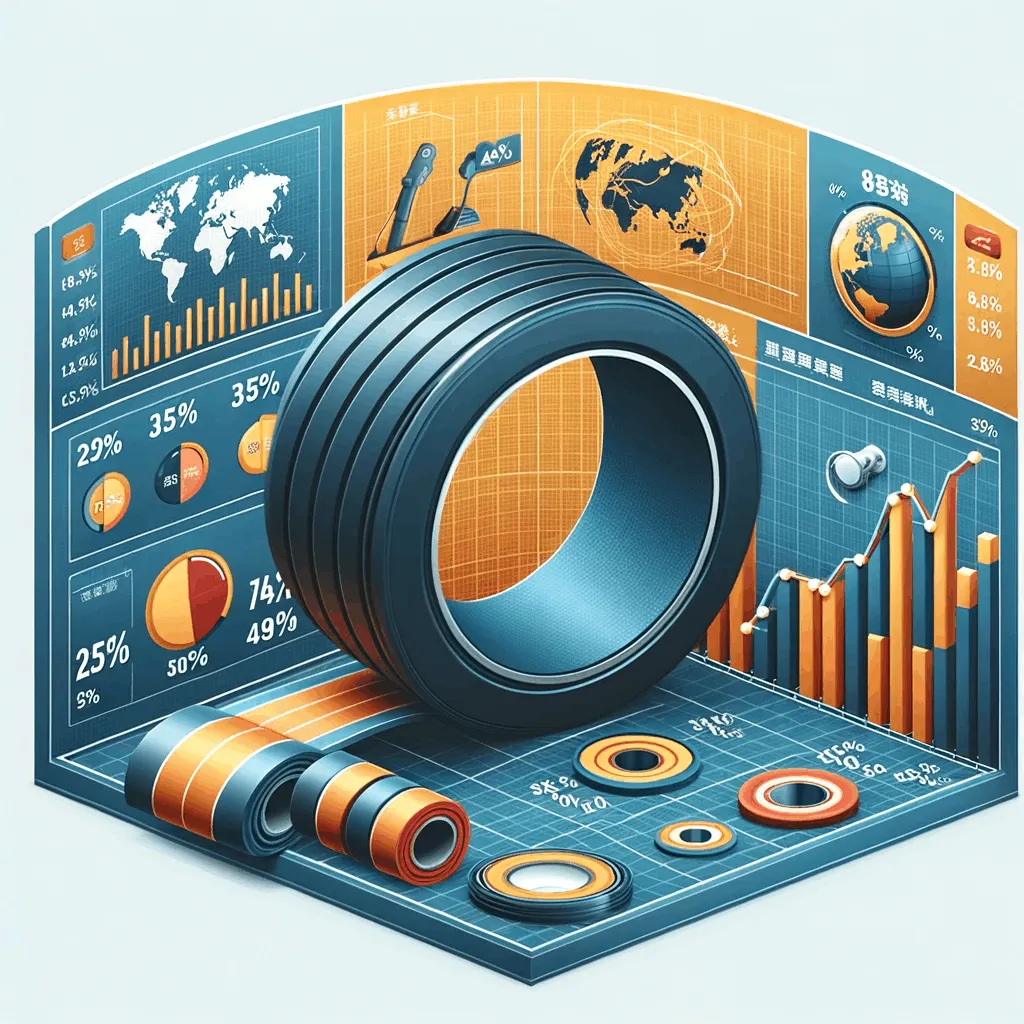
Raw Material Supply and Costs
Volatility in prices of natural rubber and synthetic blends heavily impacted production costs for manufacturers in 2022. Disruptions in Southeast Asia due to adverse weather led to supply shortfalls, while petrochemical feedstock dynamics also influenced price swings.
However as upstream investments bear fruit, most industry experts expect a stabilization trend, which should ease pressure on margins longer term. The opening of several large-scale synthetic rubber plants in China and India last year is key to improving supply stability.
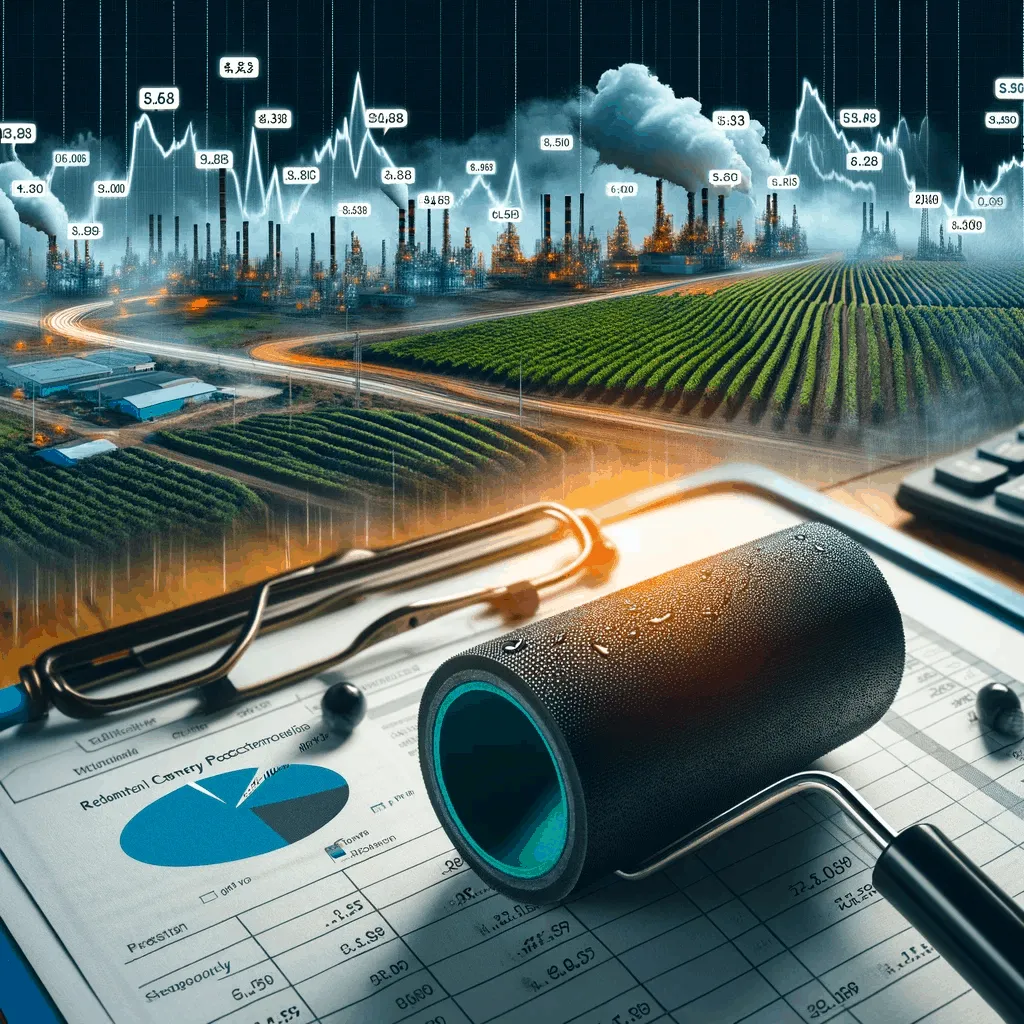
Downstream Industry Impact
While the industry enjoys overall robust growth, digitalization poses some imminent challenges. The rapid rise of digital printing is expected to partially displace offset and gravure printing - key application areas for rubber rollers. Market consultant SmithCorp estimates digital inkjet printing adoption to accelerate from current 16% market share to over 30% by 2026. Correspondingly, demand for analog printing machine parts like rollers may slow.
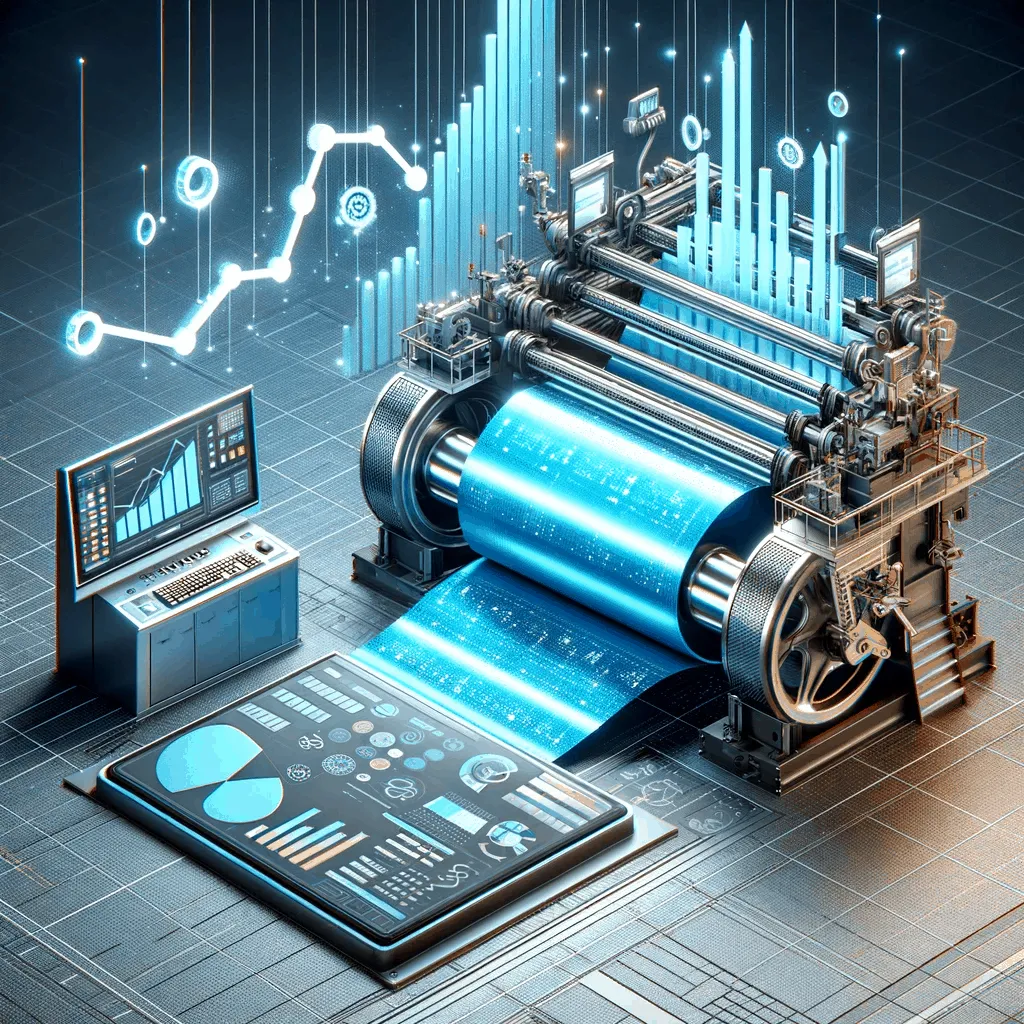
Customer Usage Shifts
In several manufacturing sub-sectors, customers are piloting use of 3D printing to replace conventional molds and machine arms requiring rubber rollers. With automotive interiors for instance, XYZ Research forecasts over 15% of components will employ 3D prints without need for custom tooling by 2025.
Such shifts towards digital direct part production, while still nascent, negatively impact market outlook for certain roller applications. Their lightweight and customizable nature also appeal to manufacturers seeking agility.
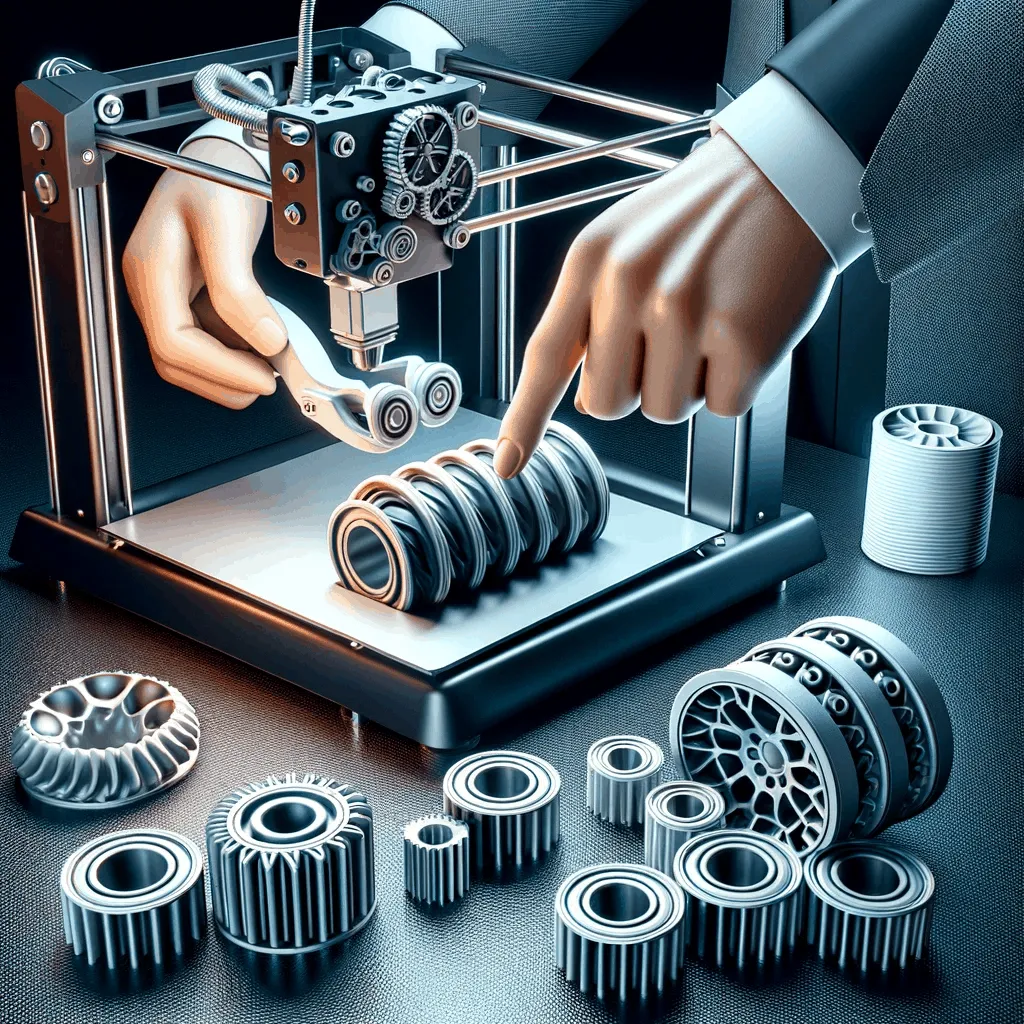
Industry Production Capacity
The global rubber roller industry remains largely consolidated amongst the top 10 manufacturers who control over 70% of total output. Leading players are actively pursuing acquisitions and capacity expansions counting on economy of scale advantages. Smaller producers however face margin pressures from rising labor and compliance costs.
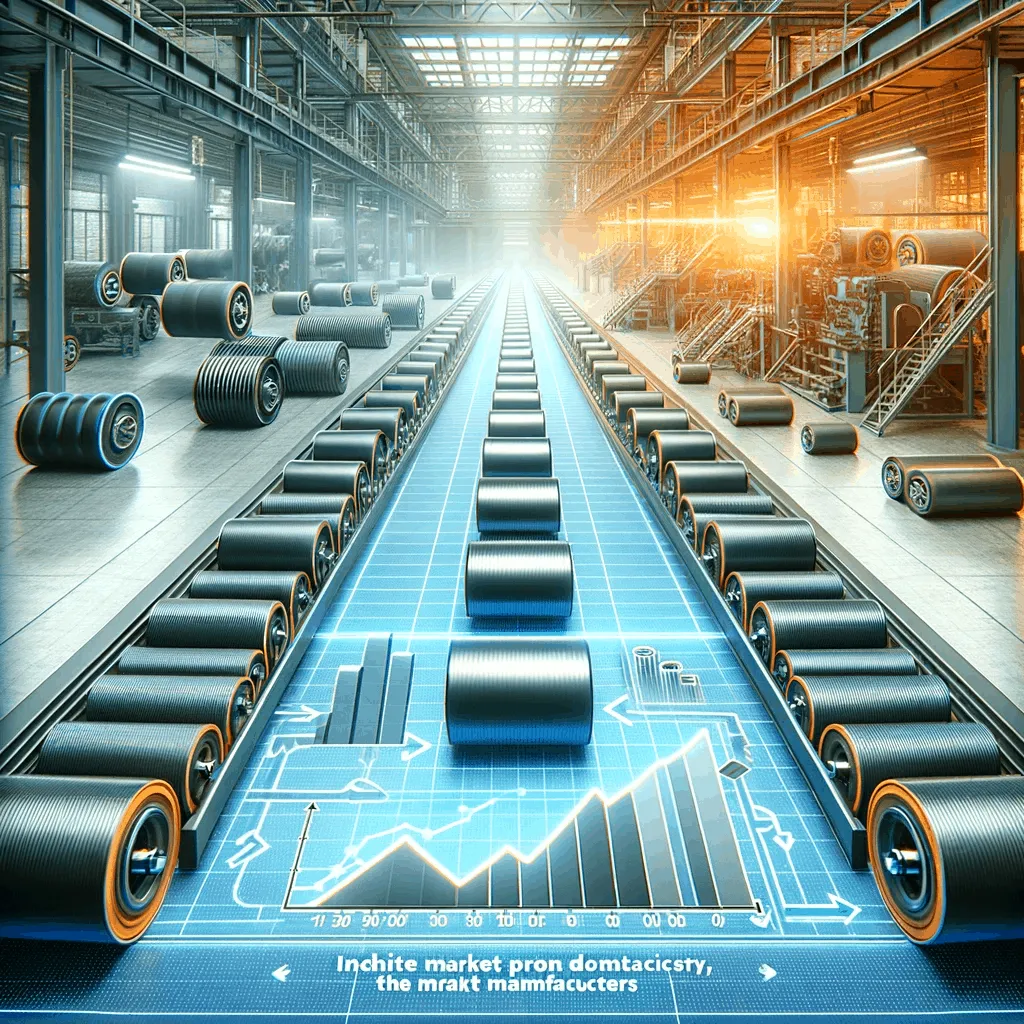
Alternative Technology Adoption
Emerging digital technologies have stimulated substitute solutions to traditional rubber rollers in some areas. For example, Company ABC's patented silicone imprinting technique incorporating pneumatic pressure mechanism now allows roller-less printing. This breakthrough greatly increases precision while reducing costs in digital printing applications.
Additionally in engineering machinery sectors, electrically heated thermoplastic conveyor belts are gaining traction to replace hot rubber rollers for sheet metal forming. Their instant heating and cooling capabilities lead to over 50% energy savings according to equipment builders. Compelling TCO advantages accelerate adoption rates.
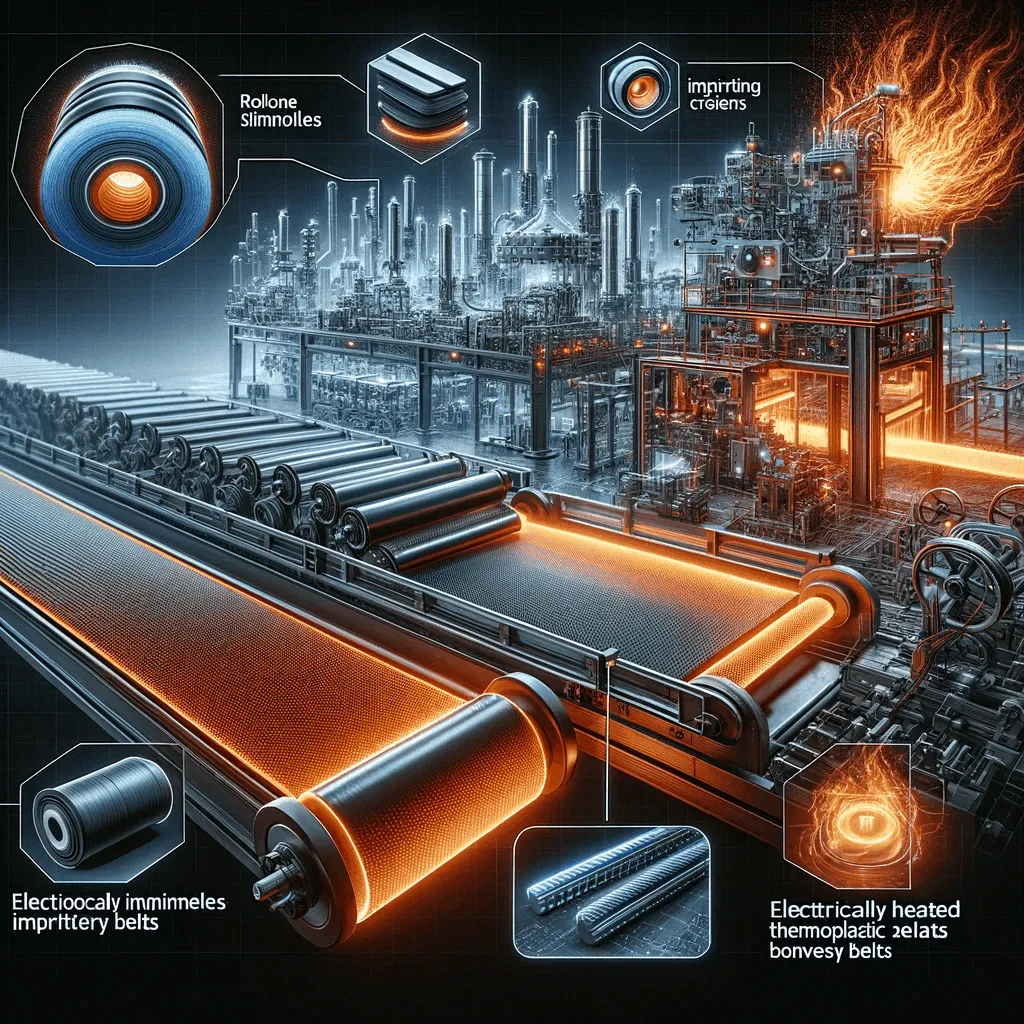
Conclusion and Outlook
The rubber roller industry retains largely positive prospects heading into 2023, underpinned by steady upstream supply factors and downstream growth drivers. However, dynamic technological shifts in key client industries prompt prudent manufacturers to prepare for scenarios of potential long term demand changes.
Forward thinking producers will monitor adoption of alternative solutions closely while redoubling R&D efforts. They may also explore M&A strategies to enhance competitiveness via economies of scale.